General
Sign up to be notified of our new blog posts.
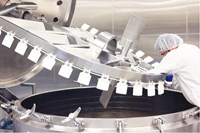
How to Prevent Downtime and Extend the Lifespan of Your Food Processing Vessels
Discover essential maintenance tips to extend equipment lifespan, reduce downtime, and lower operational costs in manufacturing.
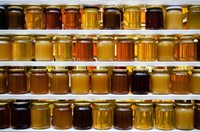
Six Tips for Food Manufacturers Purchasing Their First Mixing Vessel
For food manufacturers making the leap from small or shared-space production to expanded commercial production, processing equipment considerations can be overwhelming.
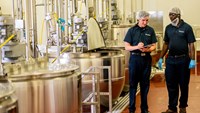
What Your Production Team Wants You to Know About Processing Vessels
Your processing vessels are used every day and are central to your operation, which means the production staff who operate your vessels learn very quickly of any shortcomings in the vessel’s design, capacity or features
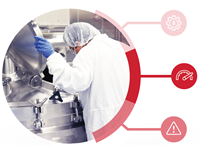
Looking Beyond Your Vessel Price Quote: What CFOs and Purchasing Managers Need to Know
It’s critically important for everyone involved in a new processing vessel purchasing decision to dig much deeper than simply the price quote. This blog covers some of the key factors that impact a vessel’s Total Cost of Ownership (TCO) over its service lifetime.

When Looking for a Vessel, Don’t Overlook the Value of a Professional Applications Engineer
In a world where you can buy anything you want from vendors you never meet in person, it’s easy to overlook the critical difference the right people—those real experts with real experience—can make on your success. This ideal is especially important for food, cosmetic, pharmaceutical, and other manufacturers looking for new processing vessels.
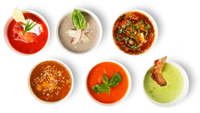
Annual Food Manufacturing Surveys Yield Important Equipment Considerations
We’re always paying attention to the issues our customers face in their businesses. That way, we can adapt our products and services to best fit their changing needs. So, the recent release of two annual research reports within the Food Manufacturing industry is particularly interesting.
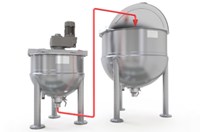
How Staggered Production Can Reduce Processing Bottlenecks
In our work with processors in key industries like food, pharmaceutical, personal care and chemicals, we often encounter production bottlenecks that can be solved with a mix of experience and creativity. One of those bottlenecks occurs when current downstream capacity can’t keep up with the desired production rate. In those situations, we’ve been able to gain significant production efficiencies by making a few equipment additions and modifying production to a staggered process: Here are a couple of techniques that have worked:
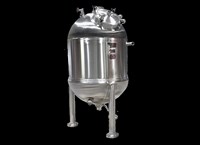
Vacuum De-Aeration: Removing Trapped Air Bubbles for Uniform Product Consistency and Accurate Dosing
Manufacturers who process high-viscosity products such as creams, lotions, ointments or gels often encounter problems with air bubbles forming in the batch, as air becomes entrained in the product during agitation. These unwanted air bubbles can prevent exact measurement and dispensing of the product in its end-use packaging, a particular problem in bio-pharma products, where highly precise dosage amounts are often required for safe and effective patient treatment.
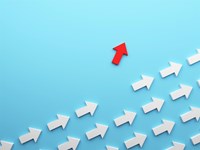
Don’t Buy the Wrong Relationship on Your Way to Buying the Right Equipment
Gather a group of experienced processing plant managers and ask them to describe their focus when deciding which supplier to buy core equipment from and you’ll hear a range of different opinions—from construction quality and durability to equipment features and performance…and price. But one recommendation they’ll likely all share is this: evaluate the equipment manufacturer’s ability to help optimize your efficiency.
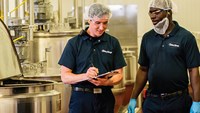
Do These Three Things Before Putting a Used Processing Vessel into Active Production
The market for used processing vessels is typically strong, due in large part to the long use life of high-quality equipment. We often see processors still using a vessel we built over 50 years ago, for example. That, and today’s high demand for new equipment, is leading even more processors to buy used equipment.
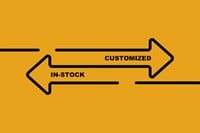
The Value of Custom-Built Processing Equipment…and What to Do If You Can’t Wait
Manufacturers that need processing equipment may have faced a similar challenge lately. While most would prefer equipment customized to their operation and product, some may feel they need to seek other options, like in-stock or used equipment. The long-term nature of processing equipment makes this a particularly important decision point: a high-quality production vessel can operate for decades.
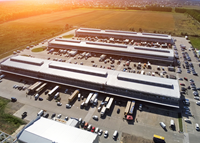
Identifying Production Bottlenecks in Process Manufacturing Operations
If you’re involved in a process manufacturing operation, you likely spend a lot of time thinking about production bottlenecks. Perhaps, if your operation is one of the many currently struggling to keep pace with increasing demand, the issue has become a top priority for you to solve.
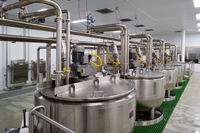
Five Equipment Decisions that Affect Efficiency and Productivity
Expansion is on the minds of many process manufacturers lately. Driven by higher demand, product innovations and new distribution channels, processors are aggressively seeking to increase production in key industries like food, pharmaceutical, personal care and chemicals.
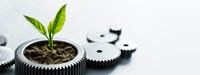
Where the Vessel is Always Greener: the Environmental Impact of Lee Products
Like many companies, Lee Industries has been examining its environmental footprint. We wanted to think harder about how the products we manufacture fit in a “greener” world. Because we believe it is important that our equipment operates in an ecologically friendly manner, we continually seek ways to engineer our kettles and tanks to minimize their impact on our environment. Here are some of the methods we use to support that goal:
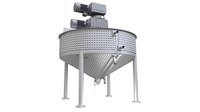
The Tell-Tale Signs of Dimple Jacket Vessel Quality
Jacketed pressure vessels – in which a jacket that surrounds a production tank is used to circulate fluid to heat or cool the vessel’s contents – are deployed throughout the food, biopharma, cosmetic, chemical and lubrication industries. For manufacturers purchasing a jacketed vessel, one of the key decisions they must make concerns the jacket’s heat transfer style.
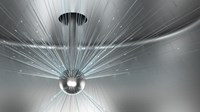
9 Vessel Design Factors that Dramatically Affect CIP Performance
Lee Industries was one of the first vessel manufacturers to introduce CIP capabilities. Since then, we’ve learned a lot about optimizing vessel design to maximize sanitary performance and operating efficiency. Here are several best practices to help you design the best CIP-ready vessel for your operation.
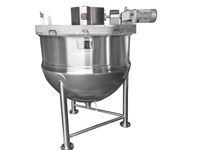
In-Stock Processing Equipment for When Custom-Built Is not an Option
Occasionally, manufacturers have an urgent need for a new vessel and don’t have the lead time required for a custom-built solution. For these situations, Lee Industries is continually manufacturing a range of our most popular models and sizes to make available as in-stock inventory upon completion. Learn more about our in-stock equipment program:
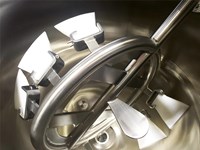
Factors That Determine the Best Agitator Design for Your Processing Operation
Processing operations involve a series of carefully engineered steps to produce, at scale, a finished product to its precise specifications. Clearly, operators that maximize the efficiency of their process and the consistency of their product gain a distinct financial advantage and more capacity to grow their business. A key contributor to accomplishing this is the operation’s processing equipment and the degree to which it is designed for the specific product and workflow.
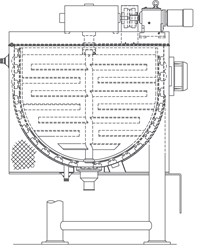
Factors That Determine the Best Processing Vessel Design for Your Operation
Knowledgeable wine drinkers know that wine glasses are designed for specific types of wines, with characteristics like shape, size, even wall thickness purposefully engineered to bring out the best in a given varietal. The difference in taste from the right vs. wrong glass style can be remarkable. The same goes for processing vessels used in food, cosmetic or pharmaceutical operations, where effectively matching product traits and operational needs to equipment design can significantly impact performance. Learn more about vessel design options in our latest blog article.
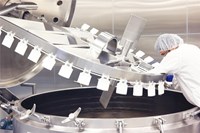
Pandemic Raises Value of Cleaning and Sanitizing Features for Processing Equipment
For food, beverage, biopharma, personal care and cosmetic product manufacturers, the need to clean and sanitize processing equipment has always been of vital importance. But in the wake of the coronavirus crisis, cleaning procedures will surely be scrutinized more heavily. Consider these equipment features to help your cleaning and sanitization efforts:
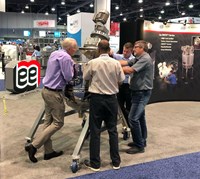
Seeing the Future of Food and Personal Care Processing: Observations from the Fall Industry Events
Every year, we spend a lot of our September and October time at industry tradeshows. We like the opportunity to see our customers, meet new people, and hear what’s on the minds of those around the industry. This year’s Fall shows for us included Process Expo in Chicago and two Las Vegas events -- the International Baking Industry Exhibition (IBIE) and PackExpo. Find out what we learned at this year's Fall shows in our latest blog article.
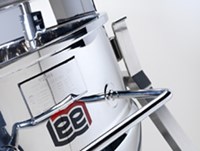
Don’t Assume Quality: The Critical Role of a Comprehensive Quality Assurance Program
We’re really picky about the quality of the kettles and tanks we build. Of course, if you rely on processing vessels in your operation, then you also need to be picky about quality, which is why we think it is helpful to understand the process we’ve developed over the years to assure the quality of every vessel before it gets delivered to the customer.
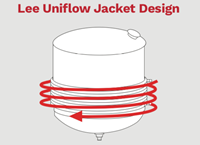
Why Do We Design Tanks with Coil Jackets?
Have you ever wondered why Lee's tanks are designed with coil jackets? See how one of the most important innovations of Lee's 90-year history makes a key difference in throughput and consistency in every batch.
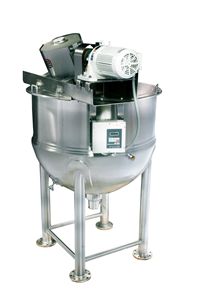
How to Make Sure the Kettle You Order is Actually the Kettle You Need
Much goes into building a high-performance processing vessel for a food, chemical or pharmaceutical manufacturing operation. Dozens of choices must be made about size, materials, mixing speeds, type of agitation, temperature, port locations, surface finishes and more. And each choice has an impact on how effectively the vessel performs in your environment. This blog article will guide your vessel design decision making and make sure you ask your process engineer the right questions.
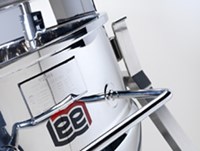
Why Surface Finish Grades are a Key Part of Your Production Vessel
The surface finish grade is a crucial but perhaps overlooked component of your production vessel. The surface finish affects more than the look of your vessel; it’s also critically important to how your vessel accomplishes its intended task — or whether it’s able to at all. A vessel’s surface finish will determine what products can be produced within that vessel. From pharmaceuticals to chemicals to food products, each industry has surface finish standards that must be met. And even beyond industry requirements, a vessel’s surface grade can have a big effect on how your product is produced.
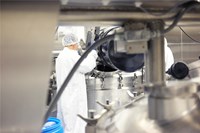
How to Meet the Challenges of High-Viscosity Mixing
Producing ointments, gels and other high-viscosity products is a challenging process. These stringently regulated products offer a high degree of difficulty for every manufacturer. Selecting the most efficient and cost-effective mixing solution can help you meet those challenges head on, but choosing the right mixing solution may be more difficult than it first appears.
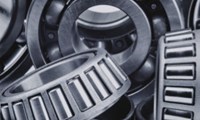
Stock Vessel Replacement Parts On-Site to Make Your Maintenance More Efficient
Keeping key parts for your Lee vessel on hand in your facility means you’ll always be prepared for both scheduled and unscheduled maintenance. Think of it as a low-cost insurance policy for your equipment. What parts should you keep on-site?
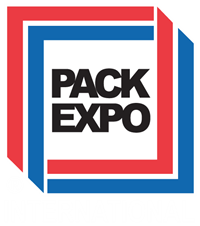
See Lee Industries Innovations in Food Processing at Pack Expo International 2018
PACK EXPO International, to be held in Chicago beginning October 14, is the biggest packaging and processing event in the world. We’re always excited to be a part of Pack Expo. Lee Industries is committed to offering the best in custom processing vessel solutions and this is a perfect opportunity to show all we can do to help our customers improve worker and product safety, increase efficiency and reach new levels of productivity.
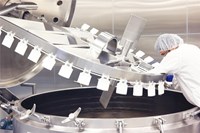
Remember Your Processing Kettles During Your Upcoming Plant Shutdown
Winter shutdowns are right around the corner. For manufacturers that depend on processing kettles and tanks, preparing for these crucial weeks becomes critically important, and not just because it’s an ideal time to take care of annual maintenance. Your winter shutdown can put your facility in a position to succeed next year—or leave you chasing maintenance issues that could have been addressed much earlier.
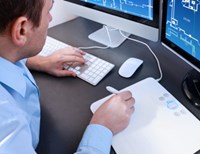
The Importance of a Clear Manufacturing Quote for Your New Processing Vessel
Obtaining a proposal for equipment you intend to use in your processing operation is a critical part of your purchase process. Here are three key benefits of a clear, easy-to-understand manufacturing equipment quote.
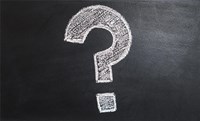
Three Questions You Should Ask Your Processing Equipment Manufacturer
Preparing to buy a new piece of processing equipment can be a daunting process, but it doesn’t have to be. Knowing the right questions to ask before you buy can put you on the path to success.
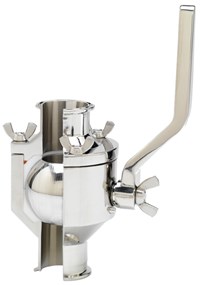
Engineering Advancements That Make Cleaning and Maintaining Your Processing Equipment More Efficient
Cleaning and maintaining processing equipment is vital for production teams in the food, beverage, bio/pharma and chemical industries, but these processes can be costly and often take up enormous amounts of time. Learn how to optimize the efficiency of your operation in this latest blog article.
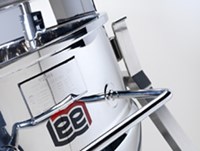
Lee Industries Receives ISO Quality Management Systems Certification
Lee Industries recently received the ISO 9001:2015 Quality Management Certification, a marker of the company’s ongoing commitment to the highest international standards of quality.