Sign up to be notified of our new blog posts.
Don’t Assume Quality: The Critical Role of a Comprehensive Quality Assurance Program
Posted on September 04, 2019
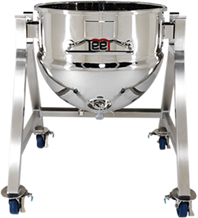
We’re always humbled by the vital role our kettles and tanks serve in our customers’ operations. Whether used for food and beverage, biopharma, cosmetic, or industrial and chemical processing, some of the world’s best products come to life in our kettles and tanks. These vessels can be the heart and soul of a processing operation and have an enormous impact on product quality and production efficiency.
So, we’re really picky about the quality of the kettles and tanks we build. Of course, if you rely on processing vessels in your operation, then you also need to be picky about quality, which is why we think it is helpful to understand the process we’ve developed over the years to assure the quality of every vessel before it gets delivered to the customer.
Pre-Fabrication Engineering is Critical
While the focus here is on fabrication quality, it must be noted that before we begin building a kettle or tank, much thought has gone into the vessel’s design and configuration. Our experienced Applications Engineers consider your product mix, near- and long-term production objectives and overall processing environment to devise a vessel to match your exact needs. From there, our Design Engineers create detailed plans and, once blueprints are approved, our focus shifts to building your vessel to the highest quality standards.A Seven-Step Quality Assurance Process
Lee Industries is ISO 9001:2015 Certified, which sets stringent requirements for a quality management system. As part of our system, a team of engineering supervisors monitors vessel fabrication throughout the process, with multiple quality checks at every step – from ordering and receiving materials to metal cutting, bending and welding to finishing. As the vessel nears completion, we use a critical seven-step process to verify its fabrication quality and accuracy.
- Manufacturing Engineer Inspection: The Manufacturing Engineer performs an initial inspection of the fully constructed vessel to verify that it meets all ASME code standards and identify any build issues or imperfections that need to be addressed. If any punch-list items are found, the vessel will return to fabrication.
- Quality Manager Inspection: Following adjustments, a Quality Manager inspects the vessel. As a second set of eyes, the Quality Manager can independently note any corrections needed.
- Manufacturing Engineer Inspection: The Manufacturing Engineer returns to re-examine the vessel and confirm all corrections have been made.
- Design Engineer Inspection: The Design Engineer who created the blueprints takes measurements and inspects the vessel against the original plans to ensure fabrication accuracy.
- Chief of Design and Manufacturing Review: This is the final fabrication review step to verify that all design specifications have been successfully met.
- Applications Engineer Review: The Applications Engineer has been involved in the project from its inception and is most familiar with the customer’s operation and end needs. They review the vessel with “customer eyes” to make sure it matches all expectations and is absolutely customer-ready.
- COO Sign Off: Because we hold ourselves accountable for the quality of the finished product, our COO inspects every kettle or tank and is the final sign-off before the vessel is released for delivery to the customer.
ASME Code Inspectors Onsite
Vessel fabrication is a heavily regulated category, so in addition to our internal quality control system, third-party code inspectors are involved throughout the construction process. In our case, we review prints and verify code calculations with onsite inspectors before releasing to fabrication and communicate fabrication status throughout the process to ensure inspectors can evaluate what they need when they need it.
For mission-critical processing equipment, the level of quality assurance attention during fabrication can have far-reaching impact, affecting everything from your delivery and commissioning timelines to your operational efficiency and scalability to your cost of ownership and durability. Clearly, those are factors to be picky about.
Read more about Quality Assurance here. Or contact us if you have any questions or challenges that we can help you solve.
Comments
Add Your Own Comment