Sign up to be notified of our new blog posts.
How to Prevent Downtime and Extend the Lifespan of Your Food Processing Vessels
Posted on December 11, 2024
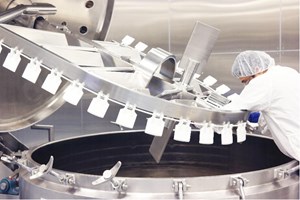
Here are two things that both corporate and plant-level people in the food industry can agree upon in today’s operating environment: 1) There is a growing need to increase capacity with current assets, and 2) To accomplish that, unplanned machine failures and shutdowns must be avoided.
For many food manufacturing operations, cooking and mixing vessels play the lead role in meeting both of those needs. Because vessel downtime affects the entire operation, it is essential to prevent it from happening or limit the impact if something does happen.
Best practice manufacturers are creating proactive vessel maintenance programs. Here are five practical strategies they use to keep their vessels running every shift for years to come:
Did you know: A recent study found that nearly two-thirds of plant operators experience either daily or weekly failures of critical plant assets that result in unplanned downtime.
1) Customize a Preventive Maintenance Schedule
There is no one-size-fits-all when it comes to scheduling maintenance for food manufacturing vessels. The unique operating factors of each operation contribute to the proper schedule. While you can use other factors as a benchmark, be sure to consider how these elements change the calculus for your operation:
The makeup of the products you produce: Are you producing high viscosity or low viscosity products? Do you use acidic or salt-based ingredients in your product?
The operational utilization of your vessels: There is a significant difference between running one shift five days per week vs. a 24/7 operation when it comes to maintenance needs.
A well-executed preventive maintenance schedule that accounts for your operational factors can help you detect and address equipment issues before they become major problems:
Routine Checks: Regularly inspect your vessel for early signs of wear and tear, such as unusual vibrations or temperature changes.
Lubrication and Cleaning: Consistently clean and lubricate parts to reduce friction, which can cause wear over time. This helps avoid operational slowdowns and extends the lifespan of each component.
This will also give you the data you need to create a proactive replacement schedule for things like driveshafts, bearings, seals and scrapers.
2) Keep Good Vessel Records
Create institutional knowledge of your vessels, so you’re not limited to any individual’s expertise or memory. Documentation of vessel maintenance, including parts lists, drawings and records of past service work, will save time and frustration and help you make better decisions when things go wrong.
3) Keep an in-house spare parts inventory
Taking a proactive approach to spare parts is particularly effective at reducing downtime and disruption. With an inventory of spare parts, there is no production delay while waiting for replacement parts to arrive. Focus your inventory on these areas:
Common wear items, like seals, bearings, scrapers and pins.
Long lead-time parts that could shut you down for an extended period if a custom replacement part needs to be fabricated, such as drive assemblies.
4) Monitor Equipment Performance
Ongoing performance monitoring helps detect subtle changes in equipment operation that could indicate future issues. By keeping a close watch on critical metrics, manufacturers can identify and address problems early. Key metrics to monitor:
Look for shifts in temperature, power consumption, noise levels, or efficiency, as these can signal developing issues.
Listen for grinding, rumbling or greater than usual vibration during mixing operations.
Look for wear on agitator scrapers, pins, and ball valve seals.
5) Plan for Downtime Strategically
While unplanned downtime is disruptive, scheduling maintenance during low-demand periods can reduce the impact on production. Planned downtime is an opportunity to perform more comprehensive checks and repairs, ensuring that equipment remains in top shape without affecting output. Top-tier vessel manufacturers offer certified maintenance checkups that can augment or support internal maintenance staff.
Given the critical role of cooking and mixing vessels in the food manufacturing operation, it is much better to build a proactive maintenance program that prioritizes awareness, inspection and preventive maintenance. In fact, such initiatives have been found to reduce downtime and maintenance costs by up to 70%.
Not only is keeping vessels in optimal working condition essential to maximize productivity and prevent costly downtime, but proper attention can add years to the vessel’s service life, delaying or eliminating the need for capital expenditures. A proactive maintenance program that prioritizes awareness, inspection and preventive maintenance can ensure that your equipment operates the way you need it to: reliably and efficiently, with minimal downtime.
To help, we’ve created a Scheduled Service Checklist that you can use to guide your maintenance program. Or, if you’d like to talk to a Lee Industries applications engineer, please contact us.
Comments
Add Your Own Comment