Sign up to be notified of our new blog posts.
Looking Beyond Your Vessel Price Quote: What CFOs and Purchasing Managers Need to Know
Posted on April 26, 2023
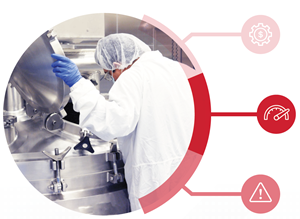
In a time of cost pressures and rising prices, the first impulse of a CFO or purchasing manager looking at a price quote for a new processing vessel is to pick the lowest bid. While this may be the right approach for some equipment purchases, the complexities of a processing vessel, and its crucial role in your operation, can turn that hope for big savings into something quite different. In reality, over the service life of a vessel, the reasons why the price of one vessel are lower than another often lead to the lower-priced option costing significantly more.
This is why it’s critically important for everyone involved in a new processing vessel purchasing decision to dig much deeper than simply the price quote.
Key factors that impact a vessel’s Total Cost of Ownership (TCO) over its service lifetime:
- Vessel material sourcing: When evaluating a vessel price quote, ask some hard questions about the material sourcing for the vessel. For example, a lower-priced vessel may be quoted using lower-cost stainless steel sourced from substandard mills, where lower-quality raw materials are regularly used in the manufacturing process. Additionally, ask to review mill certification documentation and verify its authenticity—fraudulent or non-existing certification can be used to mask inferior steel, as this thread on ENG-Tips engineering forum indicates. To avoid costly and potentially dangerous problems, always be sure the quoted vessel will be fabricated using reliably sourced, high-quality stainless steel.
- The vessel’s build quality. Build quality includes the component design and welding quality for every part of the unit—the vessel body, the agitator and drive assemblies. It is particularly important to understand the build quality of the vessel’s heating/cooling jacket, since jacket leaks are more common--and expensive and difficult to repair--in a lower-cost vessel.
- Total Cost of Ownership (TCO). This includes all related service costs over the lifetime of the processing vessel--over and above its initial cost--such as annual maintenance and parts replacement costs, and other repairs as needed. Over the more than 90 years Lee has been in business, we can say with certainty that a lower-cost vessel’s lower build quality will result in substantially higher TCO over its lifetime, and these costs must be factored into yearly equipment maintenance costs.
- Production downtime. The cost risk associated with unscheduled vessel breakdowns can often be the most expensive cost associated with a lower-priced vessel. When a vessel must be taken offline for repairs, downtime can result in lower production output and higher overtime labor costs. This downtime can possibly extend to days or weeks of delay if major components, such as a vessel’s custom driveshaft assembly, must be repaired or replaced. Just ask your production team: when factoring in every hour of lost production time in your plant, how long do they think it will take for these downtime costs to exceed the nominal initial savings from selecting the lower-cost vessel?
Choose Long-Term Value Over Short-Term Savings
The right processing vessel should provide high-quality and efficient service to your operation for decades. By exploring more than just the price within a lower-cost vessel quote and carefully considering the potential—and potentially large—additional costs which may be associated with it, your CFO or purchasing manager can make the best choice for your company.
For more information, download Total Cost of Ownership and Your Next Processing Vessel. To discuss your particular situation with a Lee Industries application engineer, just contact us. We’re happy to help you think through your needs.
Comments
Add Your Own Comment