Sign up to be notified of our new blog posts.
Factors That Determine the Best Processing Vessel Design for Your Operation
Posted on September 02, 2020
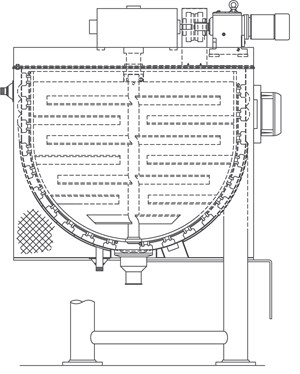
Knowledgeable wine drinkers know that wine glasses are designed for specific types of wines, with characteristics like shape, size, even wall thickness purposefully engineered to bring out the best in a given varietal. The difference in taste from the right vs. wrong glass style can be remarkable.
The same goes for processing vessels used in food, cosmetic or pharmaceutical operations, where effectively matching product traits and operational needs to equipment design can significantly impact performance.
Often, in our early discussions with manufacturers about their equipment needs, they will express preference for a certain vessel style. This may be a style they are already familiar with, one that they have seen other manufacturers use, or a style they came across in their preliminary research. Yet, as deeper conversations reveal more about their operation and objectives, we frequently find a superior solution – one that better fits their particular situation. Understanding the key inputs for those solutions can help equipment buyers more effectively manage their specification process.
The factors application engineers consider that you should too
Several factors about your product, processes, business objectives and physical facility must be considered to determine the best vessel solution for your operation. These include:
Product weight and viscosity | Heavy and thick products flow through your vessel much differently than lighter and low-viscosity products. This factor will affect decisions on vessel configuration and agitation styles to optimize mixing performance, ease of discharge and cleaning. |
Production volume | Your throughput objectives will influence your vessel capacity, and therefore your vessel style. Capacity choices must also reflect any physical space limitations, your workflow processes and personnel required. |
Product variety and variability | If you will be producing only one product in your vessel, its design can be completely customized around that product. But if you intend to produce multiple products, your vessel must accommodate more flexibility, including agitator selection and turnaround requirements for switching products. |
Ingredient characteristics | Characteristics of your product’s ingredients – e.g., delicateness, compatibility, ease of flow – affect vessel design choices due to their impact on powder addition, mixing and discharge. |
Scalability | Future growth plans must be considered in vessel design to ensure your equipment can scale with your needs. Capacity, mixing, heating and cooling performance, product discharge processes and ease of cleaning are all important elements of scalability that are influenced by vessel design choices. |
Physical space and mechanical requirements | Any limitations on space or requirements dictated by mechanicals (e.g., access to heat source) must be prioritized in your vessel design. |
Integrated processes and equipment | Unless they are part of an operational overhaul or new line, your new vessels must work within your existing production processes and the boundaries of other equipment. |
Processing vessel options: matching the design to your need
Once you have a grasp of your product and operational factors, you can begin to apply them to a range of vessel design options to determine the best solution for your situation:
Design Style | Key Design Notes | Ideal Application |
Hemispherical bottom kettle |
| Critical mixing products (e.g., delicate ingredients, hard-to-mix ingredients) Multiple product applications |
Dished bottom tank with agitation |
| Large capacity production where mixing is critical |
Cone bottom tank with agitation |
| Very high viscosity or semi-solid product Hold tank |
Pitched bottom tank |
| Water-like low viscosity with or without heat transfer |
Tanks without agitation |
| Product storage with limited mixing needs |
Beyond matching the vessel design to your needs, your vessel can be configured with an array of options and accessories to further enhance your operation. Depending on your product and business goals, these can include instrumentation, jacket type, covers, custom finishes, tilting kettles, nozzle types and customizable operator safety features.
Choosing your vessel design is a critical step for your operation. Whether you are in start-up, replacement or expansion mode, the more you understand how to match your design to your product attributes and operational characteristics the higher the return on your vessel investment will be.
Lee Industries application engineers can help you make sense of your options. Let us know if you’d like to discuss your specific situation or need more information.
Comments
Add Your Own Comment