Sign up to be notified of our new blog posts.
Improvement Opportunities Checklist
Posted on March 27, 2024
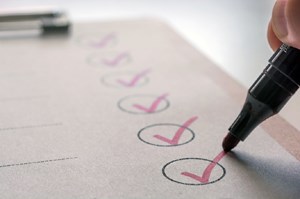
Too often, a bustling food processing facility—with goals for product quality, operational efficiency, and throughput—runs into a similar challenge, struggling to get all three.
But by looking in the right place, many operators are hitting the trifecta. Which is encouraging for food processors who want to know how the products they make today can be made better tomorrow.
These operators succeed by focusing on two key elements: the design of their production workflow and the fit between their processing equipment and their products. When in harmony, workflow and equipment make it possible to consistently optimize product quality and operational productivity in the most cost-efficient manner possible.
To help you consider if and how these elements apply to you, we’ve come up with a list of common indicators for improvement opportunities. See if you recognize any of these situations in your operation:
1. Opportunities to improve product quality
The leading cause of quality problems in food processing involves operations that sacrifice product integrity and/or consistency due to limitations of the equipment they have in place. This most often happens when production is designed around legacy equipment. Be on the lookout for these situations:
Situation | Takeaway |
Equipment capabilities are not well-matched to the product being produced. | Products that feature delicate or chunklike ingredients require a gentle cooking and mixing process to optimize and protect quality. A tank that heats quickly or uses a robust agitation system can damage such ingredients. |
Equipment trade-offs were made that sacrifice quality for versatility, so that the same vessels can be used for multiple products. | This is a particular challenge for contract manufacturers who produce a variety of products. An effectively designed system can maximize flexibility by considering all current and potential products and taking advantage of versatile heating/cooling and agitation engineering. |
It takes too long to properly mix and/or cook product. | Equipment that is not matched to your product may be able to produce the quality you seek but may not be able to deliver the volume you need. Vessel style, volume capacity and heat transfer surface area can all affect your productivity and throughput. |
Different vessel types or sizes are used to produce the same product, with varying results. | It is common for processors to rely on a mixed bag of equipment styles to produce their product. This makes consistency a real challenge, as it is very difficult to get the same finished product from different vessels with different agitation systems. |
2. Opportunities to improve product efficiency and productivity
As operations scale, adding volume and new products, the need to optimize efficiencies and maximize throughput also grows. A holistic view of how you utilize your processing vessels can uncover opportunities for improvement. Look for these situations:
Situation | Takeaway |
For your most important product, there is an ideal mixing/cooking standard that cannot be reached because the same equipment is used for other products. | For many processors with multiple products, one product dominates their production capacity. Rather than split their vessels’ use across multiple products, which interrupts production of the main product, it can be significantly more efficient to add a vessel, so that one can be dedicated for the main product while the other is shared to produce the remaining products that are less vital to the business. |
Offloading procedures must be adjusted to accommodate variations in processing time when mixing and cooking in multiple vessels. | Batches produced on multiple vessels can adhere to multiple timelines, creating inefficiencies in discharge and post-processing processes. Staggering your operation or adding a holding vessel can maximize production bottlenecks. |
Using the same production vessel for small volume pre-mixing (e.g., bases) as is used for large-volume batch processing. | Using separate smaller prep/pre-mix vessels can keep your larger vessels in constant production, accelerating production and significantly increasing throughput. |
To achieve consistency, product produced in different vessels is discharged into a collective batch and normalized. | When the only way you can mass produce a consistent product is to normalize the output from different vessels in a collective batch, that can create a significant bottleneck in your operation. Far better to deploy vessels that can mimic each other’s heating, temperature, mixing and timing to produce a consistent product in every batch. |
There are process tweaks that you would experiment with if you could separate them from your existing production flow. | You likely have ideas of how to improve your process but may have no available equipment to trial those ideas without interrupting your all-important production flow. Two options to consider: invest in a small lab version of the vessel and agitation system or work with an equipment manufacturer who can make a test lab available to their customers. |
Getting the ROI You Deserve
While solving for these situations may involve investing in some new equipment, the return can easily outweigh the cost. Whether due to better quality and consistency or increased throughput that drives additional sales revenue, or more efficient productivity that saves time and labor and frees the operation to pursue additional opportunities, the ROI is measurable and can be significant.As you consider your own situation, be sure to involve your equipment team as early in the process as possible, including your equipment vendor, even if it is just to help you identify your improvement options. The experience of applications engineers who have seen and solved similar challenges, and their expertise in designing equipment and processes around your product line, as opposed to the other way around, will help you avoid the costly problem of being at the mercy of your equipment.
Want to talk to an expert? Our Applications Engineers are a great resource and would welcome the opportunity to help you. Simply reach out to us here.
Comments
Add Your Own Comment