Sign up to be notified of our new blog posts.
How Precision Mixing Enhances Batch Consistency in Pharmaceutical Manufacturing
Posted on January 08, 2025
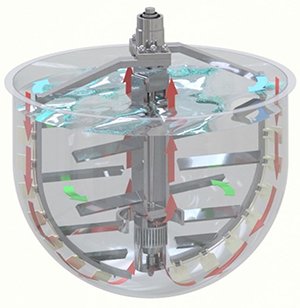
In an industry that relies on precision, maintaining uniformity is complicated by complex formulations that contain temperature-sensitive or high-viscosity ingredients. Ensuring that each batch is identical requires an efficient and consistent approach to the mixing process.
The Role of Precision Mixing in Reducing Variability
Consistency in pharmaceutical manufacturing starts with precision mixing. Proper mixing ensures that ingredients are evenly distributed, reducing the chances of separation, uneven texture or an off-spec batch. Achieving this level of consistency requires equipment purpose-built to produce identical product in every batch.
Agitators designed for pharmaceutical applications, like Lee’s Tri-Mix Turbo Shear™, are key to addressing this challenge. Systems that incorporate counter-rotating mixing bars to move ingredients efficiently around the vessel together with mechanical and/or hydraulic shears to reduce and control uniform particle size to as small as two microns, allows manufacturers to manage the mixing process with precision. Operators can adjust speeds, control temperatures and ensure that delicate ingredients are not damaged during production, assuring the final product is uniform and meets their quality standards.
Key Elements of Precision Mixing
- Controlled Mixing: Effective mixing technology enables consistent distribution of ingredients throughout the vessel, reducing the risk of uneven batches. This is accomplished via a double-motion agitator with scraper blades that clean the vessel walls during each blending revolution, then move the product toward the middle, where it is further blended by counter-rotating bars. This is particularly effective when mixing viscous products, such as thick ointments or lighter gels and hard-to-wet-out ingredients.
- Variable Speed and Gentle Handling: Adjusting mixing speeds and intensity allows for better control over the process, ensuring ingredients are combined evenly without damaging sensitive components. This is especially important for pharmaceutical products that contain delicate or heat-sensitive elements.
- Temperature Management: Maintaining consistent temperature during mixing helps preserve the integrity of temperature-sensitive ingredients. The ability to integrate controlled heating and cooling ensures that even the most sensitive formulations remain stable throughout the process.
The Importance of Reducing Variability
For manufacturers, reducing variability between batches is not just about meeting quality standards—it’s also about operational efficiency. Inconsistent batches can lead to waste, reworks or even product recalls. For pharmaceutical products, which are held to the highest standards, minor inconsistencies can lead to larger regulatory issues.
By reducing variability, manufacturers can improve the reliability of their production processes, minimize waste and increase the overall efficiency of their operations. This not only boosts confidence in the product but also reduces the risk of costly delays and quality concerns.
Consistency as a Competitive Advantage
Manufacturers that can consistently produce high-quality products at scale are better positioned to succeed in today’s ever-more dynamic marketplace that prioritizes both safety and efficacy. By focusing on precise mixing and reducing batch variability, manufacturers can improve product quality and reliability. For those looking to enhance their production processes, exploring ways to increase mixing precision can provide a significant operational return.
If you’re interested in learning more about advanced mixing solutions that support pharmaceutical production, contact one of our applications engineers. We would be happy to discuss your operational needs.
Comments
Add Your Own Comment