Sign up to be notified of our new blog posts.
Challenge Accepted: A Tight Fit
Posted on August 13, 2019
The Challenge: Fitting a 400-Gallon Vessel In a Confined Space
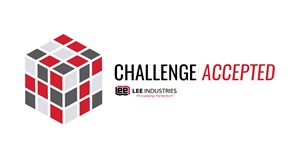
Challenge Accepted is a periodic review of how we solved a unique customer challenge.
Maneuvering around the physical constraints of a plant is a common challenge for processors. But for one of our pharmaceutical manufacturing customers, a particularly difficult space problem required a particularly innovative solution.
To keep up with growing production demands, the customer needed to add a vessel to its processing line. Regulations governing the topical manufacturing industry required that any new vessel must match the 400-gallon batch capacity and overall performance of the process that had previously been validated. Any variation from the process would trigger an extremely expensive and disruptive revalidation. This was a problem, since the customer did not have enough physical space to install and operate another 400-gallon vessel.
“We’re out of options,” the exasperated client said.
The Solution: Design Engineers Propose a Vertical Hydraulic Lift
The customer’s space restrictions limited the new vessel to a diameter narrower than a standard 400-gallon vessel. So, to achieve that volume, the vessel would have to be made much deeper than normal. Simple solution, right? Not so fast. That type of change can dramatically affect heating, cooling, agitator lift and mixing functionality. While Lee engineers were unfazed by the heating, cooling and mixing challenges – they’re quite used to managing performance in a variety of sizes and shapes –agitator lift and cleaning issues had their attention. The customer’s product was thick and sticky, meaning mixing-scrapers would have to be removed and cleaned after every batch, and the narrower, deeper design would prevent our normal agitator tilt functionality from working.
After onsite visits and several brainstorming sessions, Lee engineers devised a brilliant solution. They designed a vertical lifting hydraulic cylinder device to raise the agitator out of the vessel, then rotate it out for easy access.
While this idea made it possible for a 400-gallon vessel to operate in the confined space, a few more challenges had to be overcome to turn it into reality. For one, the facility’s ceiling was too low to accommodate the full vertical lift distance. Our solution? Mount the base of the system below the floor! Further complicating the matter, the facility’s only utility runs and hydraulics controls were located on the other side of the building. To solve that, we supplied a separate hydraulic power pack dedicated exclusively to this vessel.
The results have been spectacular. The vessel operates continuously, giving the customer the needed production capacity, while making it easy to clean and maintain. The customer also improved the accuracy of its load cell product weight measurement, as measurements are now taken with the agitator centered above the vessel.
It’s a great example of how experienced engineers with a customer-focused mindset can make good things happen. Challenge solved!
Have an engineering challenge you need to solve for your processing operation? Tell us about it.
Comments
Add Your Own Comment